Completing a Risk Assessment before the installation of a racking structure is essential to remain compliant with the Health and Safety at Work Regulations 1992 (HSE) which requires all employers to identify and assess the risks in their work environments. Conducting a risk assessment of the area enables appropriate control measures to be put in place to protect staff, and visitors as well as reduce accidental damage to stock.
But, why is this the subject of technical topics? Well, within the regulations is a clause that states, “Any assessment…shall be reviewed…if there has been a significant change in the matters to which it relates“. The installation of a pallet racking system will certainly require a reassessment of the site. The hazards that exist while building a racking system will be different to those that exist during normal business operations.
This guide put together by our team of engineers and SEIRS (Storage Equipment Installers Registration Scheme) registered installers explains the need for risk assessments and the share of responsibility when it comes to identifying hazards, the people in danger and the steps required to remove the risk so that they avoid injuries and accidents.
Want to know more? Get in touch today!
Risk Assessment Responsibilities
Your Health and Safety Officer, or Warehouse Manager will have already carried out a risk assessment to cover activity within your normal warehouse operations, covering the hazards that exist including those relating to the use of handling equipment, lorry movements and the movement of goods. The site would have been surveyed, the hazards identified, and risks recorded, and all employees will then be informed of the methods to reduce these risks.
When it comes to installing a new pallet racking system or updating a current racking system a range of new, different and unique hazards are introduced to the site. To comply with the legislation RediRack will give you our hazard and risk assessment sheets covering the equipment we will bring to the site and the working practices we will use.
Note that these vary according to the height and type of rack installation.
Interested in Learning More About Pallet Racking Safety?
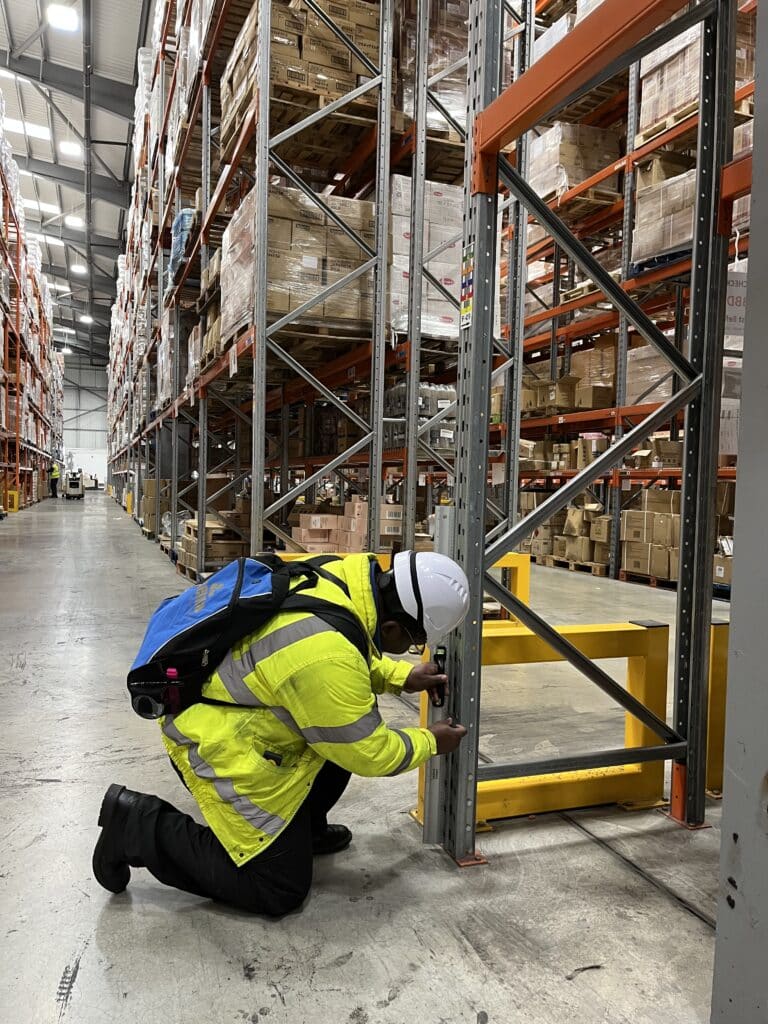
Risk Assessment Process
From our experience, the best way of working is for us to have a single contact at your company to deal with all the safety issues. This may be your Health and Safety Officer or Warehouse Manager. Our contract controller will handle all safety issues from our side.
Things we will look out for include hazards such as fire doors being blocked and constructing a mezzanine floor that gives access to a first-floor doorway before its external stairway is in place!
As our customer, you will be actively involved in this process as our presence on your site will expose your staff to new hazards.
Your responsibilities include:
- Employing a competent contractor – check out what to look out for, here.
- Being aware of what we, your chosen contractor will be doing while on your site.
- Making us aware of any special hazards that exist on your site.
- With our help, assessing the risks of having us on your site.
- Developing a method statement detailing how you will continue to work while we are on your site.
- Analysing the safety implications of having a major construction happening on your site.
- Distributing all this information to your staff.
Having followed this process, we will control and minimise the risks associated with the construction of your new RediRack pallet racking system. However, this is not the end of the process. Once the scheme is finished and operational the hazard and risk assessment must be reviewed to cover your new facility.
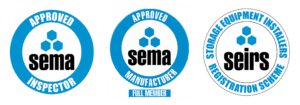
RediRack are full members of SEMA (Storage Equipment Manufacturers Association), with our installation and inspection teams fully SARI (SEMA Approved Rack Inspector), and SEIRS (Storage Equipment Installers Registration Scheme) registered.